Prototyp wielofunkcyjnej głowicy drukarki 3D umożliwiającej kontrolę jakości w czasie rzeczywistym
W ramach programu MEiN „Studenckie koła naukowe tworzą innowacje” – edycja I
Numer projektu: SKN/SP/495858/2021
Okres realizacji: 09.06.2021 – 08.10.2022
Przyznane dofinansowanie: 69.648zł
Zespół:
Jakub Bryła - Kierownik Projektu
Jan Tuptoński - modele 3D prototypu głowicy
dr hab. inż. Adam Martowicz, prof. AGH - opieka merytoryczna

Cel
Celem realizacji projektu było opracowanie, wykonanie i przetestowanie prototypu wielofunkcyjnej głowicy drukarki 3D umożliwiającej kontrolę jakości w czasie rzeczywistym. Ze względu na charakter procesu wytwarzania w technologii FDM zdecydowano o zastosowaniu kamer termowizyjnych jako czujników kontrolujących prawidłową realizację zadania druku.
Założenia projektowe i model CAD głowicy
Przed rozpoczęciem prac projektowych zespół SKN sformułował następujące założenia:
1) wielofunkcyjną głowicę przeznaczono do zamontowana w istniejącej drukarce 3D – do tego celu wybrano drukarkę 3D Ender 3v2 firmy Creality,
2) do budowy urządzenia wybrano wysokotemperaturową końcówkę roboczą (hotend) firmy E3D, model V6,
3) w celu minimalizacji masy głowicy postanowiono zastosować domyślny ekstruder (mechanizm podający filament, tj. materiał budulcowy) drukarki 3D Ender 3v2, typu Bowden,
4) w celu zapewnienia poprawnej realizacji procesu druku 3D przewidziano montaż dwóch turbin chłodzących odpowiednio radiator hotendu V6 oraz wytłaczany materiał,
5) założono, że zamocowanie wielofunkcyjnej głowicy (adapter) zostanie opracowane dla domyślnej płytki montażowej drukarki 3D Ender 3v2.
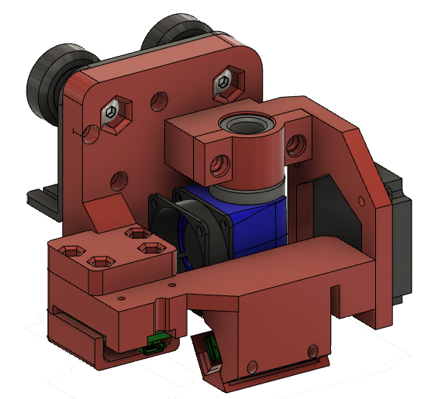
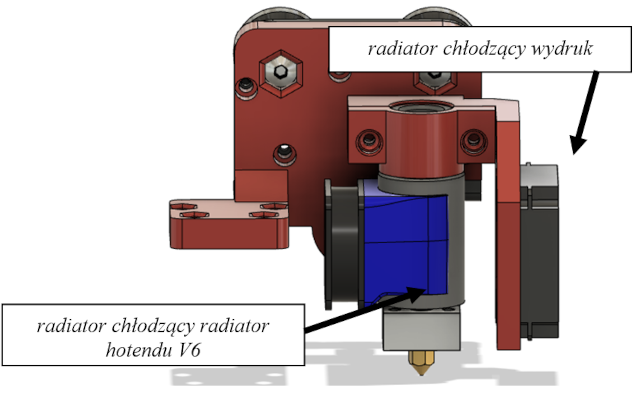
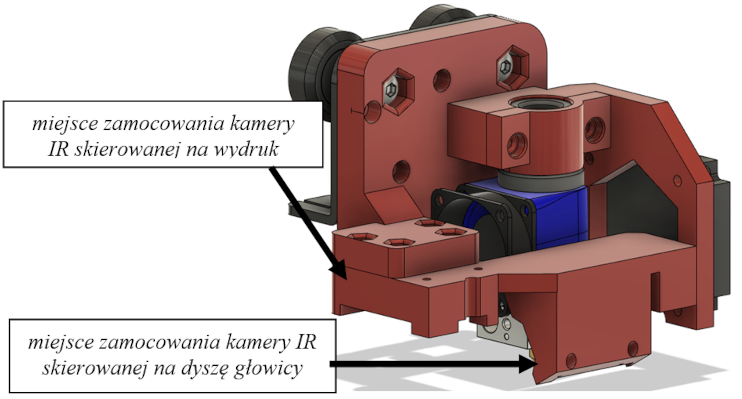
Model CAD wielofunkcyjnej głowicy drukarki 3D do kontroli jakości w czasie rzeczywistym.
Wykonanie demonstracyjnego prototypu głowicy
Zespół SKN wykonał kilka prototypów demonstracyjnych wielofunkcyjnej głowicy z materiału PLA w celu weryfikacji realizacji założeń projektowych
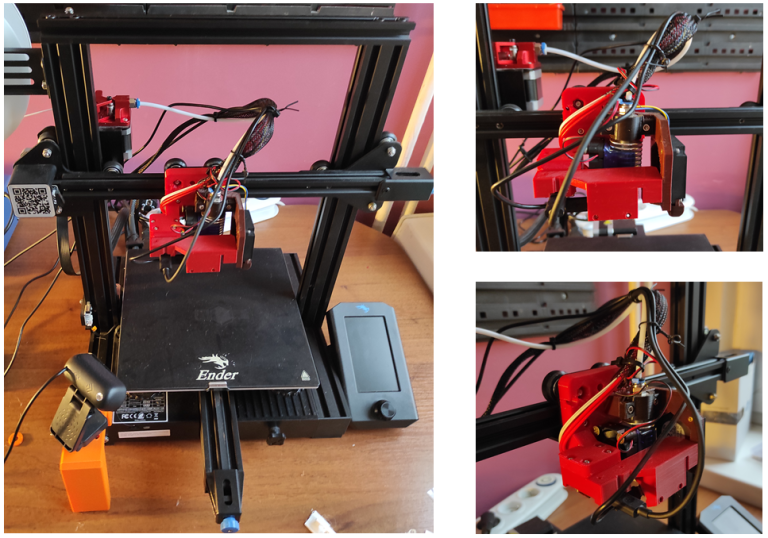
Zdjęcia demonstracyjnej wersji wielofunkcyjnej głowicy zamontowanej na drukarce 3D Ender 3v2.
Analiza rozkładu temperatury
W celu zagwarantowania bezpiecznych warunków pracy dla kamer termowizyjnych wielofunkcyjnej głowicy, zdecydowano o pomiarze pola temperatur w miejscach ich montażu. Pomiaru dokonano dla finalnej wersji demonstracyjnego prototypu za pomocą kamery Flir I7.
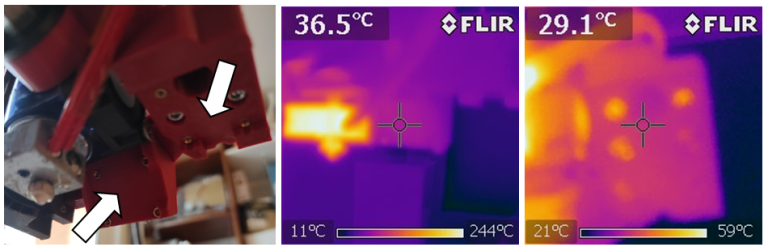
Lokalizacja miejsc pomiarowych w głowicy bez osłon dla kamer IR (po lewej),
termogramy dla obszarów mocowania kamer skierowanych na: dyszę głowicy (w środku),
oraz na wydruk (po prawej).
Prototyp głowicy w wersji finalnej
Mając na uwadze wymagania dotyczące wytrzymałości głowicy, pracy w wysokich temperaturach oraz bezpieczeństwo pracy kosztownych kamer termowizyjnych, zespół projektowy zdecydował o wykonaniu finalnej wersji prototypu urządzenia z trzech inżynierskich materiałów, odpowiednio: filamentu PA12+CF15 (producenta Fiberlogy), żywicy high Temp v2 (Formlabs) oraz żywicy ESD (Formlabs). W tym celu dokonano niezbędnej modyfikacji geometrii części głowicy w celu zapewnienia możliwości wykonania wrażliwych powierzchni urządzenia z odpowiednich materiałów.
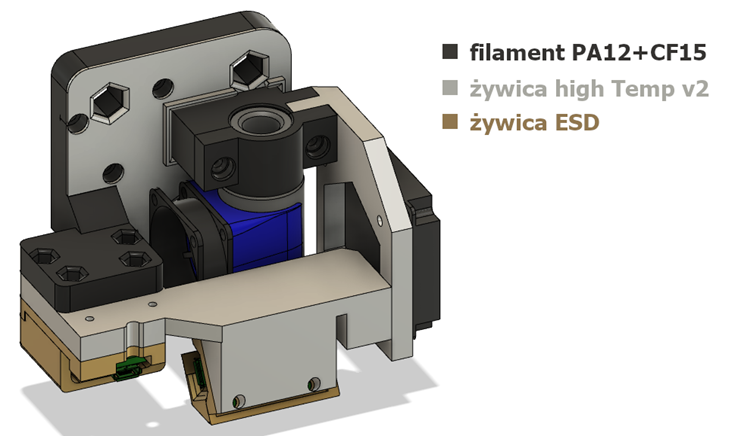
Finalny model CAD prototypu głowicy.

Zdjęcia finalnego prototypu wielofunkcyjnej głowicy zamontowanej w drukarce 3D Ender 3v2.
Testy funkcjonalności
Proces wydruku przebiegał podobnie dla każdej warstwy modelu i obejmował następujące etapy: 1) wytłoczenie ścieżek filamentu dla zadanej warstwy modelu 3D z ciągłą rejestracją obrazu z kamery termowizyjnej skierowanej na dyszę głowicy, 2) przejazd głowicy do zadanej pozycji, wykonanie zdjęcia kamerą internetową wydrukowanej warstwy, 3) przejazd głowicy nad każdy wierzchołek modelu w ostatniej wydrukowanej warstwie i wykonanie zdjęcia za pomocą kamery termowizyjnej skierowanej w stronę stołu roboczego/wydruku.
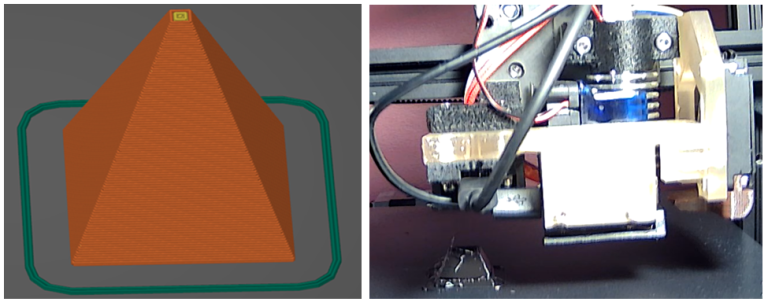
Próbny wydruk: zrzut ekranu z programu PrusaSlicer przedstawiający wizualizację drukowanego modelu (po lewej), głowica w trakcie pracy (po prawej).
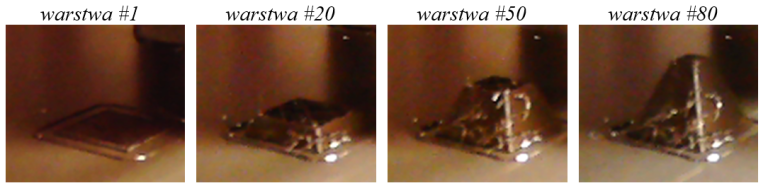
Zdjęcia wydrukowanych wybranych warstw testowego modelu 3D.
Eksperymenty z kontrolowanym wywołaniem awarii w trakcie druku
W ramach testów głowicy zrealizowano kontrolowane wywołanie wybranych typów awarii procesu druku 3D oraz poddano ocenie możliwość wykrycia niepoprawnego przebiegu procesu wydruku. Poniżej przedstawiono wyniki uzyskane dla przypadku oderwania się drukowanego elementu od stołu roboczego drukarki.
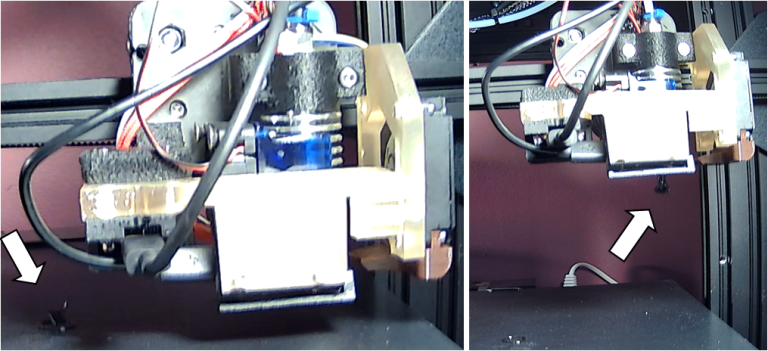
Ostatnia poprawnie zrealizowana warstwa wydruku (po lewej) oraz podniesiona głowica z przyklejonym do dyszy wydrukiem oderwanym od stołu drukarki (po prawej).
Podczas eksperymentu nastąpiło oderwanie się wydruku od stołu drukarki 3D i przyklejenia do dyszy głowicy. Przypadek ten jest szczególnie niebezpieczny. Pozostawiona bez nadzoru drukarka 3D może wówczas ulec poważnym uszkodzeniom lub może dojść do zapalenia się wydruku przyklejonego do głowicy – ilość filamentu zgromadzonego wokół rozgrzanej dyszy szybko się zwiększa wraz z postępującym procesem druku. Następnie przeprowadzono ocenę możliwości identyfikacji, w oparciu o termogramy, oderwania się wydruku od stołu roboczego drukarki 3D. W pierwszej kolejności porównano zdjęcia wierzchołków obrysu warstwy wykonane kamerą termowizyjną skierowaną w stronę stołu roboczego, tj. w stronę drukowanego elementu. Jako referencję przedstawiono termogramy dla poprawnie wykonanego elementu.
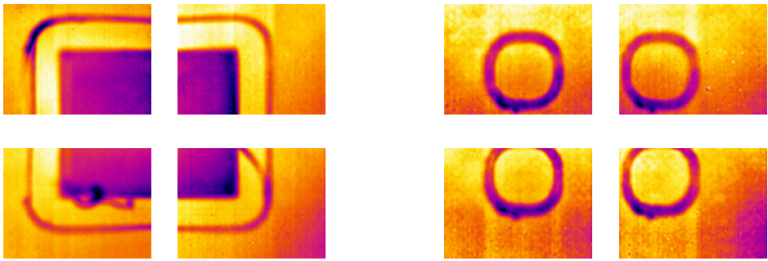
Porównanie zdjęć wierzchołków obrysu dla wybranej warstwy: dla poprawnie wykonanego elementu (po lewej) oraz dla elementu, który oderwał się od stołu roboczego drukarki 3D (po prawej).
Na zdjęciach z kamery termowizyjnej skierowanej w stronę stołu roboczego można zaobserwować chłodniejsze obszary, w których zlokalizowane są wydrukowane warstwy modelu 3D. Dodatkowo widoczna jest obwódka z pierwszej warstwy druku 3D, tzw. skirt. W przypadku odklejonego elementu widoczny jest tylko obrys (skirt). W przypadku małej powierzchni pierwszych warstw wadliwie wykonanego wydruku 3D wykazanie awarii procesu druku 3D z zastosowaniem kamery termowizyjnej skierowanej na dyszę jest kłopotliwe.
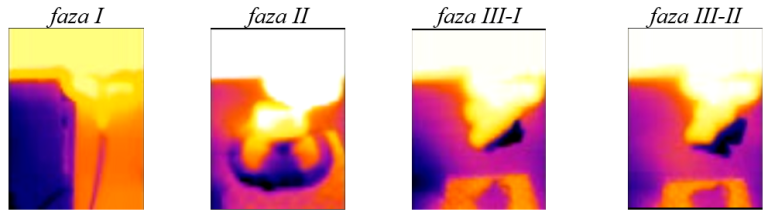
Obrazy kolejnych etapów druku 3D zarejestrowanych przez kamerę termowizyjną skierowaną na dyszę głowicy.
W pierwszej fazie procesu druku zaobserwowano nagrzewanie dyszy. W drugim kroku głowica wytłaczała filament, poprawnie odwzorowując geometrię modelu 3D. Podczas fazy III-I nastąpiło przyklejenie się wydruku do dyszy głowicy. W skutek dalszej ekstruzji materiału, tj. podczas fazy III-II, element przyklejony do głowicy stopniowo powiększał swoją objętość. W trzecim etapie można zaobserwować chłodniejsze fragmenty wydruku przyczepionego do dyszy na skutek działania wentylatora, którego docelowym zadaniem jest chłodzenie wytłaczanego filamentu.
Montaż głowicy w drukarce 3D wysokotemperaturowej
Finalnie dokonano montażu prototypu wielofunkcyjnej głowicy w wysokotemperaturowej drukarce 3D. W tym celu wykonano dodatkowy adapter umożliwiający podłączenie projektowanego urządzenia do drukarki Creatbot F430.
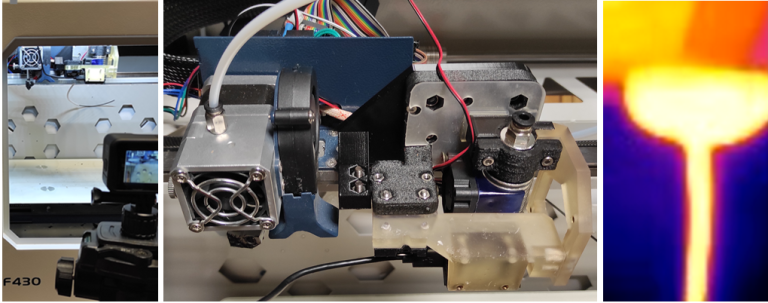